SENSY’s load limitation for hoisting devices range enables displays to be connected to indicate lifted loads to operators. Solutions are based on one or more load cells, one overload protection device with analogical or digital output, and a display for installing in the operator’s pendant or under the trolley.
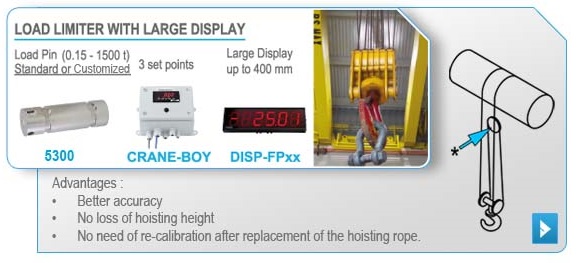
Available in 4 or 6 digits, with digit heights between 57 and 400mm (2.25 to 16” and higher on demand) with 4-20mA or RS485 entry, and allowing for long-distance communication through the crane festoon without any perturbation from power supply cables, the displays will act as repeaters of loads displayed on the overload monitors.
The accuracy of displayed loads will depend on the choice of sensor model and load monitor. For 5% uncertainty or more at full scale, wire rope load cell model 5500 combined with BRIDGE BOY will suffice for a very competitive budget.
If you are looking for 1-2% accuracy, load pin at the dead-end or upper sheave/balancing beam, combined with a digital overload protection system from the CRANE-BOY family will be the right fit.
For accuracy better than 1%, the same combination of load pin + CRANE-BOY and calibration by linearisation will enable this level of uncertainty to be attained. Linearisation: teaching the CRANE-BOY the output signals of the load sensor at different loads by lifting known loads successively with an increasing weight.
Eventually, for 0.25% to 0.1% accuracy, a weighing system based on four compression load cells installed between the trolley frame and a second frame holding the whole lifting cinematic, with one load cell at each corner of this second frame will be necessary. The four load cells are connected in parallel to the CRANE-BOY through a junction box and CRANE-BOY has to be calibrated by linearization, as described above.
This solution with multiple load cells for accurate weighing is a safety device for overload protection which means a positive safety function is vital for each of the four load cells. For this positive safety function, the junction box JBOX-LCI will carry out individual monitoring of the load cells as well as programmable unbalance detection. Both the junction box and the load cells are powered by the CRANE-BOY.
General rules for load displaying on an electrical overhead travelling crane (EOT):
- Always check the displayed load when lifting – displayed values while lowering a load might increase even though the load remains unchanged due to the sheaves factor and dynamic effects.
- Reset the display before lifting (Tare function).
- Determine the ‘reference’ height at which considering the displayed load as a significant amount of wire rope fall can cause considerable offset depending on the position of the hook block, due to the weight of the wire rope fall applied on the sensor – a weighing system with double frame and compression load cells is not subject to a hook block position as everything is weighed by the load cells.
- Take into account the displayed load when the hoist is static.