Several countries have passed laws protecting hoisting equipment against overload. There are two things at stake: for crane operators and people operating in the vicinity of a crane or overhead crane (EOT crane), this is about safety; for the corporation owning the lifting system, it is about the sustainability of the equipment and controlling maintenance costs.
At present, structural designs are optimised in terms of mechanical resistance and thus the amount of raw material to allow for competitive sales pricing. Incorrect use of hoisting device includes lifting loads above the crane’s nominal capacity which accelerates the wear and tear on the machine and fatigue of crane components like sheaves (pulleys), hook block or spreader, gearbox, dead end anchor point and service brake, etc. This is also valid for the crane wire rope for which recurring operations under overload will speed up its wear and replacement cycle.
At present, structural designs are optimised in terms of mechanical resistance and thus the amount of raw material to allow for competitive sales pricing. Incorrect use of hoisting device includes lifting loads above the crane’s nominal capacity which accelerates the wear and tear on the machine and fatigue of crane components like sheaves (pulleys), hook block or spreader, gearbox, dead end anchor point and service brake, etc. This is also valid for the crane wire rope for which recurring operations under overload will speed up its wear and replacement cycle.
Although most new cranes are currently being commissioned with overload protection devices, there are still plenty of cranes which are not equipped with such load-limitation systems.
Often, when laws on overload protection do not exist, corporations tend to delay investment in safety equipment because of the corresponding costs. SENSY’s programme for load limitation systems for hoisting devices offers a broad range of technical solutions with costs related to the selected solution. If a production EOT crane deserves an appropriate solution, hoists with low capacity and/or scarce use (such as a hoist in a maintenance shop) do not need such a ‘high-end’ solution with higher costs.
For those cranes which do not require a solution with load pin (Clevis pin) and multiple function load limitation monitor (overload protection, slack rope detection, pre-alert, interdiction of opening coil transport tool, etc.) and load display, SENSY offers a long-proven range of wire rope load cells (clamp on rope) and cost-effective analogical overload protection monitors.
SENSY model 5500 – to be clamped on the rope at the dead-end anchor point or close to the upper sheave, while keeping an eye on installing the sensor so that it does not collapse into the pulley during the lifting movement – offers a large range of transducer sizes covering wire rope diameters from 6 to 46mm (0.236 to 1.811”) and nominal loads at dead end from 0.25 to 24 metric tonnes.
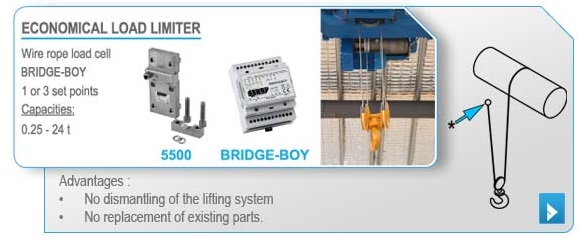
The BRIDGE BOY-1R overload monitoring device is an analogical module charged with protecting the concerned hoist against overload. It ensures hoisting safety requirements thanks to its positive safety function (overload relay trips when load cell signal is lost), its test button to assess overload relay function without having to lift a live overload, and overload relay tripped when measurement chain is not powered.
Quickly commissioned (cell clamped on wire rope, monitor installed, overload relay connected in serial with upper limit switch), easily calibrated with live loads, the EOT crane concerned will be upgraded within half a day.
In the case of EOT cranes with two or more hoists, the BRIDGE-BOY limiter has analogical output for communication with a summing module to avoid overloading the crane when the sum of hoists exceeds the crane’s nominal capacity. A crane with two trolleys will use the BRIDGE BOY SUM module while for those with more than two hoists, CRANE-SUMD will fulfill the combined load overload protection.